Specialist Suggestions on What is Porosity in Welding and Exactly How to Resolve It
Specialist Suggestions on What is Porosity in Welding and Exactly How to Resolve It
Blog Article
Porosity in Welding: Identifying Common Issues and Implementing Finest Practices for Prevention
Porosity in welding is a pervasive concern that often goes unnoticed till it creates substantial issues with the integrity of welds. This common problem can endanger the strength and longevity of welded structures, positioning safety risks and leading to pricey rework. By understanding the origin causes of porosity and executing effective avoidance strategies, welders can significantly improve the high quality and dependability of their welds. In this conversation, we will check out the key aspects adding to porosity formation, examine its detrimental effects on weld performance, and go over the most effective techniques that can be taken on to minimize porosity event in welding procedures.
Common Root Causes Of Porosity
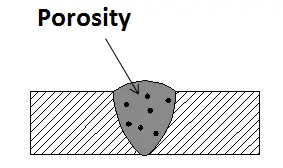
An additional regular wrongdoer behind porosity is the presence of contaminants externally of the base metal, such as oil, oil, or corrosion. When these contaminants are not effectively eliminated prior to welding, they can evaporate and become caught in the weld, causing flaws. Making use of dirty or damp filler products can present pollutants right into the weld, adding to porosity issues. To alleviate these usual sources of porosity, detailed cleaning of base steels, appropriate shielding gas option, and adherence to optimum welding specifications are important techniques in accomplishing premium, porosity-free welds.
Impact of Porosity on Weld Quality

The existence of porosity in welding can dramatically compromise the architectural honesty and mechanical residential properties of welded joints. Porosity develops voids within the weld metal, deteriorating its total toughness and load-bearing capability. These gaps function as stress and anxiety concentration factors, making the weld more prone to cracking and failing under used tons. Furthermore, porosity can decrease the weld's resistance to corrosion and various other environmental variables, better diminishing its longevity and efficiency.
Welds with high porosity degrees tend to show lower influence strength and decreased ability to flaw plastically before fracturing. Porosity can restrain the weld's capability to effectively transfer pressures, leading to early weld failure and potential safety hazards in important frameworks.
Ideal Practices for Porosity Prevention
To enhance the architectural integrity and top quality of bonded joints, what certain procedures can be executed to decrease the event of porosity Check Out Your URL throughout the welding procedure? Porosity prevention in welding is essential to make certain the integrity and toughness of the final weld. One efficient practice appertains cleaning of the base steel, article removing any pollutants such as rust, oil, paint, or moisture that can bring about gas entrapment. Making sure that the welding devices remains in great condition, with clean consumables and ideal gas flow rates, can additionally considerably decrease porosity. Additionally, preserving a secure arc and managing the welding parameters, such as voltage, existing, and take a trip speed, aids develop a regular weld pool that reduces the danger of gas entrapment. Making use of the proper welding technique for the certain product being bonded, such as readjusting the welding angle and weapon setting, can even more prevent porosity. Regular assessment of welds and immediate removal of any type of problems identified during the welding procedure are crucial techniques to stop porosity and generate top quality welds.
Significance of Proper Welding Techniques
Executing proper welding techniques is vital in guaranteeing the architectural integrity and high quality of bonded joints, constructing upon the foundation of reliable porosity prevention procedures. Extreme warm can lead to increased porosity due to the entrapment of gases in the weld pool. In addition, using the ideal welding specifications, such as voltage, existing, and take a trip rate, is essential for achieving audio welds with very little porosity.
Additionally, the selection of welding procedure, whether it be MIG, TIG, or stick welding, should align with the details demands of the job to ensure optimum outcomes. Proper cleansing and prep work of the base metal, along with choosing the appropriate filler material, are also important elements of skillful welding methods. By adhering to these ideal methods, welders can lessen the risk of porosity development and produce high-grade, structurally sound welds.

Evaluating and Quality Control Steps
Examining procedures are vital to find and prevent porosity in welding, making sure the strength and durability of the last item. Non-destructive testing methods such as ultrasonic screening, radiographic testing, and visual inspection are typically used to determine prospective issues like porosity.
Post-weld examinations, on the various other hand, examine the final weld for any kind of problems, consisting of porosity, and confirm that it meets specified requirements. Executing a thorough quality control plan that consists of extensive testing treatments and evaluations is extremely important to decreasing porosity issues and making sure the general top quality of bonded joints.
Verdict
To conclude, porosity in welding can be a typical problem that impacts the high quality of welds. By recognizing the typical causes of porosity and executing best practices for prevention, such as proper welding techniques and testing actions, welders can learn the facts here now make certain premium quality and reputable welds. It is vital to prioritize avoidance methods to reduce the incident of porosity and keep the integrity of welded structures.
Report this page